Industrial Machinery Maintenance: Best Practices to Boost Efficiency, Safety, and Equipment Life
Advertisement
When I walk through a bustling factory floor I know that every machine plays a crucial role in keeping production moving. Even the most advanced equipment can’t run forever without a little care. That’s why industrial machinery maintenance isn’t just a routine task—it’s the backbone of any efficient operation.
I’ve seen how regular upkeep can prevent costly breakdowns and keep everything running smoothly. It’s not just about fixing things when they break; it’s about making sure problems don’t happen in the first place. With the right maintenance strategies I can help extend the life of machinery and boost productivity across the board.
Understanding The Importance Of Industrial Machinery Maintenance
- Maximizing Equipment Lifespan
I always prioritize routine maintenance to extend the usable years of machinery. Following manufacturer guidelines for lubrication, calibration, and cleaning directly counters wear and tear. For example, regular oil changes in hydraulic presses keep systems running longer and smoother.
- Preventing Unplanned Downtime
I consistently schedule inspections and minor repairs to stop unexpected failures. Using predictive maintenance tools like vibration analysis, I spot faulty bearings in conveyor systems before they cause shutdowns. These checks reduce sudden halts that can paralyze factory operations.
- Boosting Productivity and Efficiency
I optimize machine performance by keeping parts aligned and components clean. Reliable equipment means I avoid production slowdowns—like bottlenecking at packaging lines due to jammed motors—so targets stay on track and customers get their orders on time.
- Lowering Operational Costs
I invest in regular service to save on expensive emergency repairs and part replacements. Detecting air leaks in pneumatic lines or changing filters in cooling systems reduces energy waste and the need for costly overhauls.
- Ensuring Workplace Safety
I inspect safety guards, emergency stops, and alarm systems during maintenance routines. By doing so, I minimize risks for operators, reducing the chance of workplace accidents common with malfunctioning equipment like forklifts or stamping presses.
- Meeting Compliance and Regulatory Standards
I maintain records of service and inspections as part of industry compliance. Staying up to date with maintenance logs helps me meet OSHA and ISO certifications, preventing fines and ensuring safe, legal operations.
Establishing A Preventive Maintenance Program
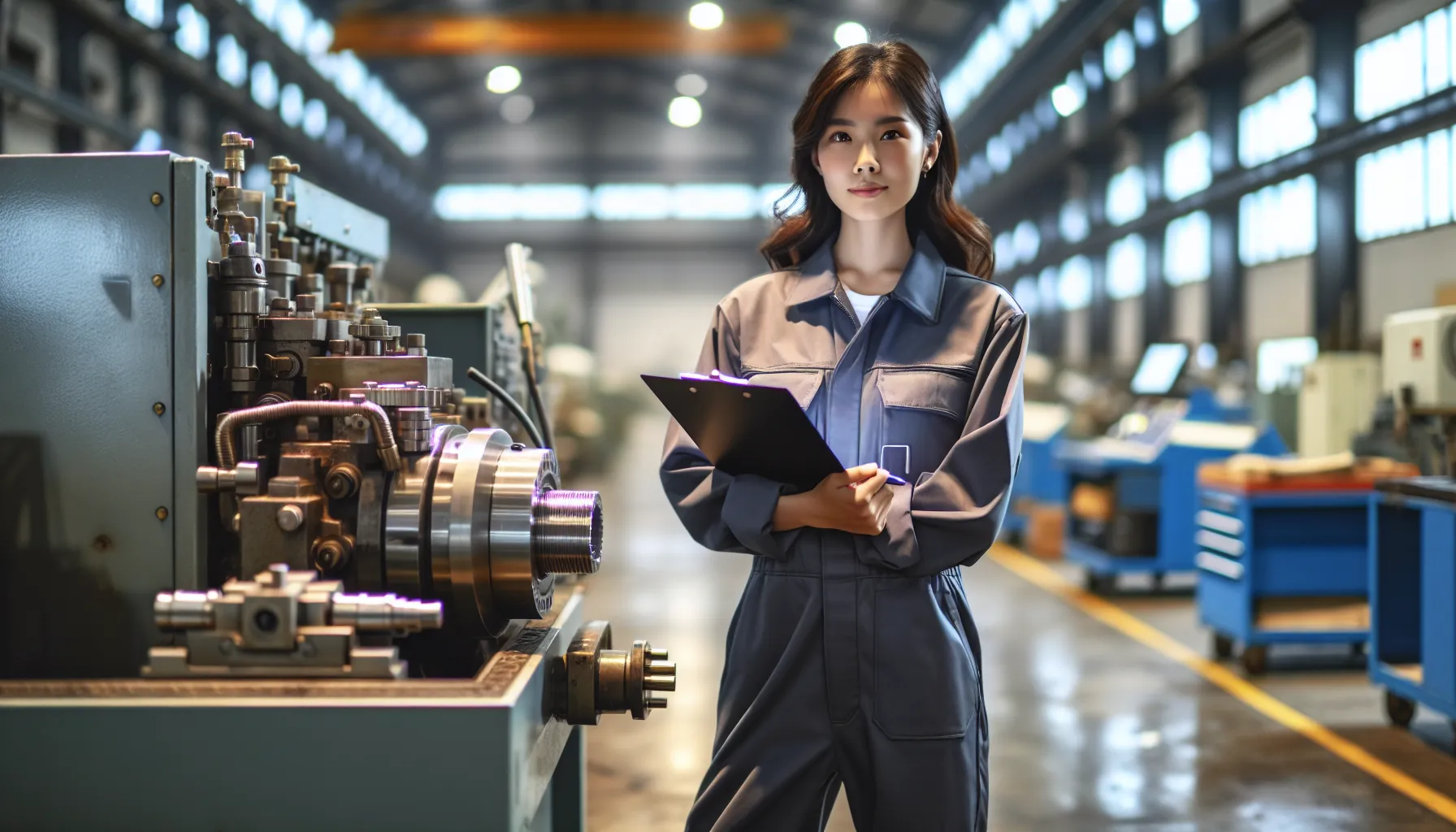
Building a preventive maintenance program lets me reduce downtime and save on costly repairs. I rely on structured processes that keep every aspect of machinery care consistent and efficient.
Scheduling Routine Inspections
Scheduling routine inspections helps me catch issues before they cause disruptions on the factory floor. I set inspection intervals based on manufacturer guidelines, usage intensity, and criticality of equipment. I use digital calendars or maintenance management software to schedule checkups for gears, belts, lubrication points, and safety components. I assign specific team members to each inspection to make sure nothing’s overlooked. Regular scheduling keeps equipment running at peak efficiency and prevents surprises.
Developing Maintenance Checklists
Developing maintenance checklists ensures that every step of preventive care gets covered. I customize checklists for different machine types, including daily, weekly, and monthly tasks like lubrication, cleaning, filter changes, and safety checks. I prioritize items based on failure history and OEM recommendations. I revise each checklist as new issues emerge or after system upgrades, using feedback from technicians. With checklists in place, my team maintains consistency, reduces errors, and provides documentation for audits and compliance.
Implementing Predictive Maintenance Techniques
Predictive maintenance saves money and prevents failures by identifying machine issues before they worsen. I rely on data-driven insights and modern diagnostic tools to keep machinery operating at peak efficiency.
Utilizing Condition Monitoring Tools
I use condition monitoring tools like vibration sensors, infrared thermography, and oil analysis kits to track machine health in real time. Vibration sensors detect imbalances and misalignments in rotating equipment. Infrared cameras help me spot overheating components in motors, bearings, and electrical panels. Oil analysis reveals contamination and metal wear in gearboxes and hydraulic systems. These tools give me actionable data, so I can schedule repairs before breakdowns cause production stops.
Analyzing Data For Early Warning Signs
I review collected maintenance data through analytics software that monitors trends and identifies deviations. I watch for patterns in temperature spikes, abnormal vibration frequencies, or changes in lubricant quality. I set custom alarms in monitoring systems, so I get notifications as soon as parameters cross safe thresholds. By acting on these early warning signs, I stop minor problems from turning into expensive failures and keep machinery running longer.
Training Personnel For Effective Machinery Maintenance
I consider well-trained personnel essential for reliable industrial machinery maintenance. I regularly invest in both safety instruction and ongoing education to keep my team skilled and adaptable.
Providing Safety Training And Best Practices
I start all maintenance onboarding with comprehensive safety training. I teach procedures like lockout/tagout, personal protective equipment usage, and emergency shutdowns using real-world examples from my facility. I organize hands-on sessions to reinforce best practices, including machinery-specific hazard identification for equipment like hydraulic presses and conveyors. I review OSHA guidelines with my team to ensure compliance and minimize accident risks.
Offering Continuous Education On New Technologies
I schedule regular workshops on emerging tools, such as predictive maintenance apps, IoT sensors, and condition monitoring software. I partner with manufacturers and bring in certified trainers to demonstrate setup, calibration, and diagnostics. I encourage online courses and webinars so my staff stays current on industry advancements, from AI-based analytics to smart lubrication systems. I maintain a habit of cross-training team members on new equipment, maximizing flexibility while reducing skill gaps in my operation.
Addressing Common Industrial Machinery Maintenance Challenges
Every facility faces obstacles that threaten machine reliability and uptime. I’ve found that meeting these challenges head-on makes my maintenance strategy stronger and more sustainable.
Tackling Wear And Tear Issues
I regularly check moving parts for early signs of wear, like excessive vibration, odd noises, or increased heat around bearings and gears. I use high-quality lubricants and stick to the manufacturer’s lubrication schedule, which keeps friction to a minimum and limits grinding on surfaces. I rotate and replace parts on a set maintenance calendar—for example, swapping out belts and filters quarterly to avoid gradual degradation. I log all maintenance actions in a digital system, so I can review trends in part replacements and spot recurring weak points. By analyzing this data, I target root causes—like misalignment or improper load handling—and retrain staff on proper operation when necessary.
Preventing Unexpected Equipment Failures
I deploy predictive maintenance tools like vibration analysis, thermal imaging, and oil condition monitoring to spot anomalies before they trigger breakdowns. I also configure sensors and alarms on critical assets, so I’m alerted instantly when data exceeds safe thresholds—such as overheating in electric motors or hydraulic pressure drops. I use scheduled inspections and testing, especially before peak production periods, to double-check that safety interlocks and emergency stop systems are functional. I review failure data with my team after every incident, then update maintenance procedures and checklists to prevent repeats. By building proactive habits and leveraging real-time data, I keep surprise outages at bay and safeguard ongoing operations.
Leveraging Technology For Streamlined Maintenance
Technology lets me optimize industrial machinery maintenance for speed, accuracy, and efficiency. By embracing digital tools, I keep my operation running smoothly while reducing manual effort and unexpected downtime.
Integrating Maintenance Management Software
Implementing maintenance management software centralizes all my service records, work orders, and inspection checklists. I use platforms like IBM Maximo, Fiix, or UpKeep to schedule preventive maintenance, track parts inventory, and assign tasks without endless paperwork. Automated alerts remind me about upcoming maintenance dates, while digital logs simplify audits and compliance. Real-time dashboards show equipment status across the facility, letting me spot bottlenecks or overdue tasks instantly.
Adopting IoT Sensors And Automation
Equipping machines with IoT sensors gives me 24/7 visibility into their health. Sensors track temperature, vibration, pressure, and energy consumption—vital metrics for early fault detection. For example, I place vibration detectors on rotating machinery or temperature probes on motors to get instant alerts when readings drift off normal. Automated data collection means I don’t miss early warning signs. Integrating sensors with control systems also lets me automate basic maintenance actions, like auto-lubrication or remote machine shutoff, making my maintenance routines more proactive and less reactive.
Conclusion
Maintaining industrial machinery isn’t just about keeping equipment running—it’s about building a culture of reliability and safety. By prioritizing skilled training and embracing technology I make sure my operations stay ahead of unexpected issues and costly downtime.
With the right tools and a proactive mindset I can adapt to new challenges and keep productivity high. Investing in maintenance pays off not just in smoother workflows but in peace of mind for everyone on the factory floor.
Frequently Asked Questions
Why is regular maintenance important for industrial machinery?
Regular maintenance helps prevent costly breakdowns, extends equipment lifespan, and ensures that machines operate efficiently and safely. It also reduces unplanned downtime by addressing potential issues before they escalate.
What are some best practices for factory machinery maintenance?
Best practices include following manufacturer guidelines for cleaning and lubrication, scheduling routine inspections, performing minor repairs promptly, and keeping detailed maintenance records for compliance and audits.
How does predictive maintenance benefit factories?
Predictive maintenance uses data and condition-monitoring tools to identify issues early. This approach saves money, reduces downtime, and prevents failures by allowing for timely repairs based on real-time machine data.
Why are maintenance records important?
Maintenance records help factories meet compliance and regulatory standards. They provide documentation for audits and help track machine performance, repairs, and scheduled maintenance tasks over time.
How does training impact the effectiveness of maintenance teams?
Ongoing training ensures technicians remain skilled and adaptable, helping them handle advanced machinery and adopt new technologies like predictive maintenance tools. Well-trained staff minimize errors and improve machinery reliability.
What technologies are commonly used in modern machinery maintenance?
Common technologies include maintenance management software (like IBM Maximo or Fiix), IoT sensors for real-time monitoring, predictive maintenance apps, vibration analysis tools, and thermal imaging cameras.
How can factories reduce unplanned downtime?
Factories can reduce downtime by implementing a preventive maintenance program, conducting regular inspections, using predictive maintenance tools, and responding quickly to early warning signs from analytics and monitoring systems.
What tools help monitor machine health in real time?
Tools like vibration sensors, infrared thermography, and oil analysis kits provide continuous data on machine condition, enabling maintenance teams to detect and address issues before they cause failures.
How can maintenance programs improve workplace safety?
Routine inspections and scheduled maintenance help ensure that safety features are functioning properly, reducing the risk of accidents. Proper training and adherence to safety protocols further enhance workplace safety.
What challenges do factories face in machinery maintenance?
Common challenges include dealing with wear and tear, preventing unexpected failures, training staff on new equipment, and managing maintenance schedules. Using digital tools and proactive strategies helps address these issues efficiently.