Industrial Machinery Parts: Types, Maintenance Tips, and How to Choose the Best Components
Advertisement
When I step onto a factory floor the sheer scale and complexity of industrial machinery always amazes me. Every moving part plays a crucial role in keeping operations running smoothly and even the smallest component can make a big difference in performance and efficiency.
Understanding industrial machinery parts isn’t just for engineers or mechanics—it’s essential for anyone looking to boost productivity and minimize downtime. I know that when a single part fails it can bring an entire line to a halt. That’s why I believe it’s so important to know what makes these machines tick and how to keep them in top shape.
Understanding Industrial Machinery Parts
The right machinery parts keep factory lines moving and production efficient. I always notice how quickly operations can stop when even one essential part fails.
Key Definitions of Industrial Machinery Parts
Industrial machinery parts include all components—large and small—that make machines operate in factories, refineries, or warehouses. I define core parts as items like gears, bearings, valves, belts, pumps, and motors. I consider auxiliary parts to be connectors, fasteners, seals, and sensors that support the main system. I regularly see these parts classified by their role: moving parts (e.g., conveyor rollers), control parts (e.g., switches), and structural parts (e.g., frames). I often hear the term “OEM” (Original Equipment Manufacturer) when companies want exact replacements for these parts, while “aftermarket” refers to third-party or alternative components that fit existing machinery.
Importance of Quality Machinery Parts in Industry
Reliable machinery parts cut downtime and boost productivity. I always prefer sourcing high-quality parts since they increase machine lifespan and reduce safety risks. I’ve noticed quality bearings, for example, extend the maintenance intervals for conveyor systems, and premium seals stop leaks in high-pressure pumps. I rely on trusted suppliers because defective parts can cause catastrophic failures, unplanned shutdowns, and costly repairs. I’ve calculated that industries using certified machinery parts usually report lower equipment failure rates, helping them meet tight production deadlines and safety standards set by authorities like OSHA and ISO.
Categorizing Types of Industrial Machinery Parts
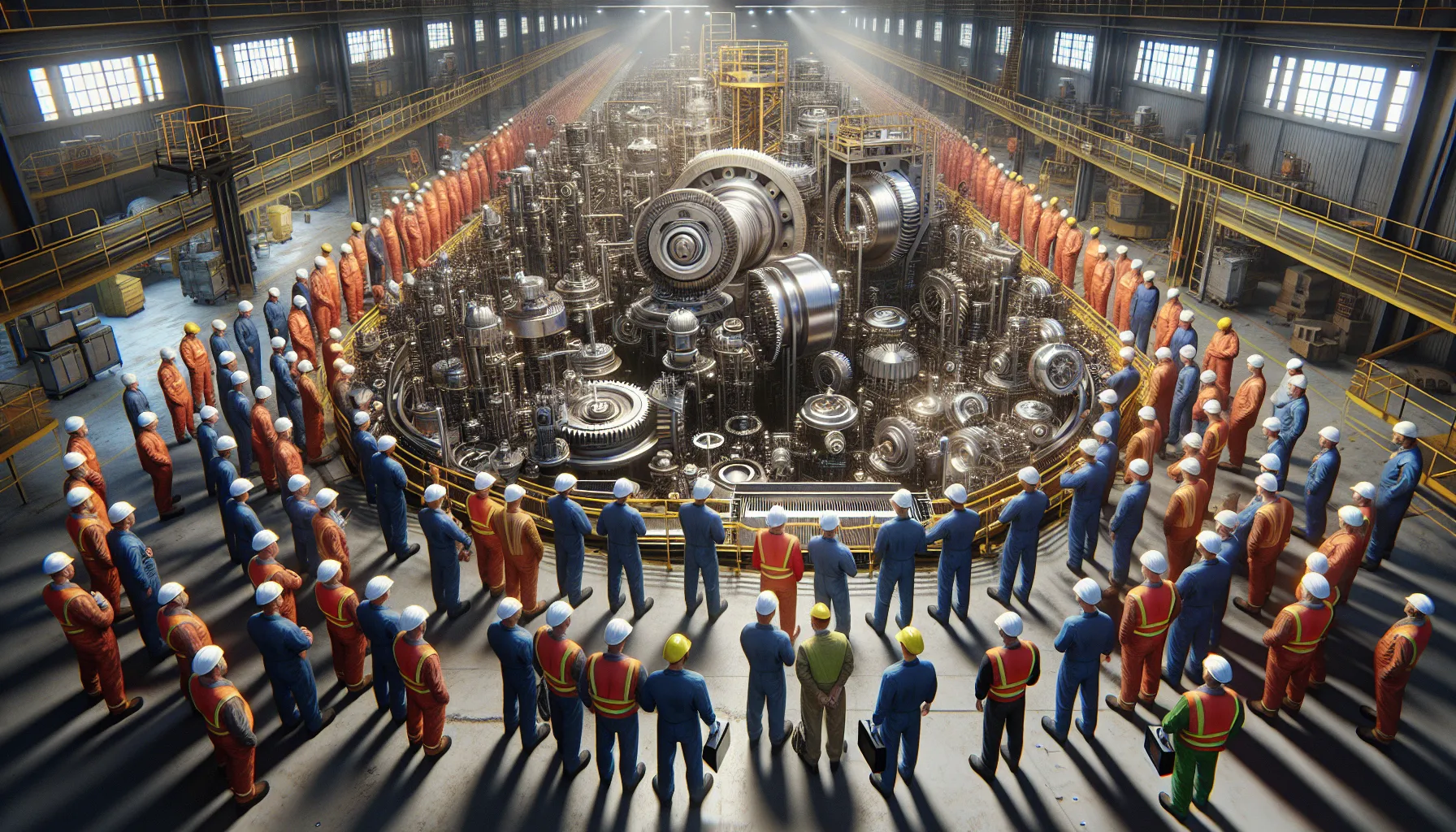
I see industrial machinery parts falling into clear groups based on their function and design. Understanding these categories helps me troubleshoot and select the right components for any application.
Mechanical Components
I rely on mechanical components like gears, shafts, bearings, belts, and pulleys to transfer motion and force smoothly. Gears, for instance, change speed or direction in conveyors or presses. Bearings support rotating shafts in pumps and motors, cutting friction. Belts and pulleys drive fans or mixers in assembly lines, ensuring consistent power transfer.
Electrical Components
I find electrical components crucial for powering, controlling, and automating machines. Motors convert electrical energy into motion in robotics and conveyor belts. Switches, relays, and circuit breakers control power flow and protect systems from overload. Sensors detect position, temperature, or pressure in CNC machines and packaging equipment, sending feedback to PLCs for precision control.
Hydraulic Components
I depend on hydraulic components like pumps, valves, hoses, and cylinders for heavy lifting and precise movement. Pumps generate necessary pressure in stampers and injection molding machines. Valves regulate flow in automated presses, while cylinders handle tasks like clamping, bending, or lifting in manufacturing lines.
Pneumatic Components
I use pneumatic components such as compressors, actuators, valves, and air filters for fast, repetitive motion. Compressors drive pneumatic tools and packaging machines. Actuators move parts in pick-and-place robots. Valves manage airflow, while air filters keep systems free of contaminants in food processing and electronics assembly.
Choosing the Right Industrial Machinery Parts
I always treat selecting industrial machinery parts as a strategic process, since each decision directly affects reliability, lifespan, and productivity.
Factors to Consider Before Purchasing
I prioritize durability when comparing parts, making sure to review the material quality and manufacturing process for bearings, seals, and belts. I check supplier reputations, actively seeking reviews from industries using similar gearboxes or hydraulic pumps. I consider lead times, especially for custom or rare gears, since unexpected delays can cost thousands per day in lost productivity. I always verify warranty coverage and after-sales support so I can address motor or sensor failures quickly. I compare prices, but focus on value by weighing longevity, certifications, and proven effectiveness in past installations.
Role of Compatibility and Standardization
I ensure components meet machinery requirements for both physical fit and operational specs, reducing risk of performance drops. I confirm compatibility with existing electronics and pneumatics—like matching sensors with controller protocols or valves with system pressure ratings. I select parts built to international standards such as ISO or ANSI whenever possible, guaranteeing cross-brand interchangeability and easier future upgrades. I rely on standardized spare parts for simplified inventory, cutting downtime by having compatible connectors, hoses, and switches ready on-site.
Maintaining Industrial Machinery Parts
Keeping industrial machinery parts in peak condition extends equipment lifespan and minimizes costly downtime. I’ll share proven maintenance strategies and highlight key warning signs that help me decide when replacement is necessary.
Best Practices for Regular Maintenance
- Conduct scheduled inspections on critical machinery parts such as gears, bearings, and belts. I spot issues sooner by sticking to a routine checklist.
- Lubricate moving components like shafts, rollers, and chains as specified by the manufacturer. I use only recommended lubricants to avoid damaging sensitive mechanisms.
- Clean dust and debris from sensors, electrical connectors, and hydraulic lines regularly. I prevent contamination that leads to electrical or hydraulic failures this way.
- Tighten fasteners, clamps, and couplings on mechanical assemblies periodically. I make sure nothing gets loose enough to cause vibration or misalignment.
- Calibrate sensors, motors, and valves based on usage hours. I guarantee precise control by confirming each part meets operational standards.
Signs of Wear and When to Replace Parts
- Notice unusual noises or excessive vibration in motors, pulleys, and gearboxes. I replace components immediately if I hear persistent grinding or rattling.
- Spot visible cracks, fraying, or deformation on belts, hoses, and seals. I don’t hesitate to swap these parts before leaks or breakdowns occur.
- Detect temperature spikes on bearings or overheating in hydraulic pumps. I use infrared thermometers to catch these early and schedule a swap-out.
- Find recurring faults in sensors, switches, or actuators despite resets. I consider these strong signals that a replacement is due.
- Track increased cycle times or reduced output precision in production machinery. I act fast to replace worn gears and actuators that compromise efficiency.
By following these best practices and responding quickly to wear indicators, I keep my machinery running smoothly and reliably.
Sourcing Industrial Machinery Parts
I find that efficient sourcing of industrial machinery parts makes all the difference in minimizing downtime and keeping factory lines on schedule. Consistent access to quality components helps ensure safety, reliability, and longevity of equipment.
Trusted Suppliers and Manufacturers
I always look for suppliers with established track records, proven certifications, and transparent supply chains. Brands like Siemens, ABB, and SKF have global reputations for quality, supporting their products with documentation and technical support. I check if suppliers offer traceability on critical parts—such as bearings, motors, and control units—to reduce the risks of counterfeiting. When I work with authorized distributors, I’m more likely to receive genuine parts, manufacturer warranties, and reliable after-sales support. It’s smart to read peer reviews, request references, and verify industry-specific certifications before committing to a supplier.
Evaluating Aftermarket vs OEM Parts
I assess whether to invest in original equipment manufacturer (OEM) parts or choose aftermarket alternatives for each application. OEM parts come directly from the original manufacturers, ensuring perfect compatibility and warranty protection, particularly for complex assemblies like hydraulic pumps or PLC modules. Aftermarket parts often provide cost benefits and faster delivery times, especially for standard components—like belts, seals, or filters—but may differ in material quality or tolerances. My rule: for critical, high-risk machinery, I select OEM components; for non-essential or standardized machines, reputable aftermarket options can be a practical choice if they meet strict quality standards and certifications.
Innovations in Industrial Machinery Parts
Industrial machinery parts evolve fast, transforming how I see reliability and efficiency on factory floors. I’ll explain key breakthroughs that reshape how these parts work, last, and connect within modern production lines.
Advances in Material Science
New alloys increase part durability and reduce friction. For example, ceramic-coated bearings and titanium alloys withstand higher temperatures and resist wear in high-speed applications.
Polymer composites lighten heavy components. I use reinforced polymers in gears and housings to cut machine weight while preserving strength, which trims energy consumption and eases installation.
Nano-engineering enhances surface treatments. My experience with nano-lubricants and coatings shows they prevent corrosion and improve sliding surfaces, sharply extending part lifespan, especially in harsh environments.
Smart Parts and Industry 4.0 Integration
Sensor-embedded parts enable real-time monitoring. I rely on smart bearings and hydraulic valves that report temperature, vibration, or pressure, letting me catch failure risks before breakdowns happen.
Wireless connectivity boosts preventive maintenance. My use of IoT-enabled motors and actuators means factory management systems receive instant updates, so they schedule maintenance automatically and avoid costly surprise failures.
Predictive analytics drive smarter operations. Cloud-integrated sensors on key parts feed usage data, empowering me to forecast wear trends and align spare parts inventory, which reduces downtime and streamlines supply chains.
Improving Industrial Efficiency with Quality Parts
I know that using quality industrial machinery parts is the foundation for efficient, reliable factory operations. Every upgraded or well-chosen component directly affects machine performance, lifespan, and the safety of everyone on the floor.
Impact on Equipment Longevity
I always notice longer equipment lifespans when I invest in high-quality parts. Genuine or certified replacements minimize premature wear, lower vibration, and resist corrosion, which means less downtime for unplanned repairs. For example, hardened steel gears and ceramic bearings maintain precision over millions of cycles, while advanced seals and lubricants shield moving parts from contaminants and overheating. Superior components also hold tighter manufacturing tolerances, preventing misalignment and unnecessary friction, so my machinery operates smoothly for years. I see fewer major overhauls and improved return on investment with every maintenance cycle.
Influence on Workplace Safety
I’ve found that quality parts are critical for workplace safety on any shop floor. Reliable brakes, emergency stops, and fail-safe switches immediately respond under stress, reducing accident risks during fast-paced shifts. Certified electronic and pneumatic parts, like sensors and valves, always react within specified tolerances, so there’s less chance of malfunction-caused injuries. For example, reinforced hydraulic hoses and shatter-resistant guards prevent leaks, bursts, and flying debris, while properly insulated wiring lowers the risk of electrical fires. Every time I use parts that meet international safety standards, I help ensure my staff stays protected, insurance costs stay manageable, and compliance audits go smoothly.
Conclusion
My experience with industrial machinery parts has shown me just how much the right components can shape the success of any operation. Staying informed about new technologies and best practices makes all the difference when it comes to keeping machines running at their best.
Choosing quality parts and maintaining them properly isn’t just about avoiding breakdowns—it’s about building a foundation for safer, more efficient, and more reliable production. By making smart decisions and staying proactive, I know I can help any operation reach its full potential.
Frequently Asked Questions
Why is understanding industrial machinery parts important?
Knowing the parts of industrial machinery helps improve productivity, reduces downtime, and enables faster troubleshooting. Understanding each component’s role ensures efficient maintenance and lowers the risk of unexpected breakdowns.
What are the main types of industrial machinery parts?
Industrial machinery parts are categorized as mechanical (gears, shafts, bearings), electrical (motors, switches, sensors), hydraulic (pumps, valves), and pneumatic (compressors, actuators) components. Each category serves specific functions to power, control, or move machinery.
How do high-quality machinery parts benefit factory operations?
High-quality parts last longer, reduce the risk of failure, and minimize downtime. They also improve productivity, boost machine lifespan, and help maintain workplace safety by preventing accidents caused by faulty components.
What should I consider when buying industrial machinery parts?
Focus on durability, compatibility, material quality, supplier reputation, warranty coverage, and after-sales support. Ensuring parts meet international standards also helps with easier integration and future upgrades.
What are the best practices for maintaining industrial machinery parts?
Regular inspections, timely lubrication, cleaning sensors and hydraulic lines, tightening fasteners, and calibrating components based on usage are essential. Promptly addressing warning signs like unusual noises and visible wear helps prevent costly breakdowns.
Which warning signs indicate machinery parts need replacement?
Look for unusual noises, visible wear, temperature spikes, recurring faults, and decreased output precision. These signs suggest a part may fail soon and should be checked or replaced to avoid larger issues.
How are innovations improving industrial machinery parts?
Advances in material science—like stronger alloys and polymers—and nano-engineered surfaces boost durability. Smart components with embedded sensors enable real-time monitoring and predictive maintenance, helping factories run more efficiently.
How does using certified and genuine parts impact safety?
Certified and genuine parts reduce accident risks, help maintain compliance with safety standards, and lower insurance costs. They improve equipment reliability and support smooth compliance audits, protecting both workers and operations.
Why is standardization important in industrial machinery parts?
Standardized parts ensure compatibility, ease of replacement, and quicker repairs. This reduces downtime, streamlines inventory management, and supports easier upgrades as technology advances.