Industrial Machinery Repair: Essential Tips to Prevent Downtime and Extend Equipment Lifespan
Advertisement
When a factory grinds to a halt because of a broken machine every minute counts. I know how crucial it is to get things running again fast. Industrial machinery repair isn’t just about fixing equipment—it’s about keeping entire operations on track and avoiding costly downtime.
I’ve seen firsthand how even a minor issue can snowball into major delays if it’s not handled right away. That’s why understanding the basics of industrial machinery repair matters to anyone involved in manufacturing or production. With the right approach it’s possible to extend the life of your machines and keep your business moving forward.
Understanding the Importance of Industrial Machinery Repair
- Identifying Early Warning Signs
I always watch for early warning signs like unusual noises, excessive vibration, or sudden drops in performance. Noticing these changes helps me catch issues before they lead to bigger breakdowns.
- Minimizing Downtime and Production Losses
I reduce expensive production losses by scheduling routine repairs and inspections. Proactive repair prevents unplanned equipment stoppages that can halt entire assembly lines.
- Extending Equipment Lifespan
I maximize my machinery’s lifespan by repairing worn-out parts, lubricating moving components, and replacing faulty sensors as needed. Regular upkeep can add years to gearboxes, conveyors, and pumps.
- Maintaining Workplace Safety
I prioritize safety by addressing malfunctions in brake systems, electrical wiring, or hydraulic lines as soon as I spot issues. Safe machinery reduces the risk of workplace accidents.
- Protecting Investment Value
I preserve my company’s investment by ensuring assets remain in optimal working condition. Well-maintained industrial machinery maintains higher resale and trade-in values.
Identifying Common Industrial Machinery Issues
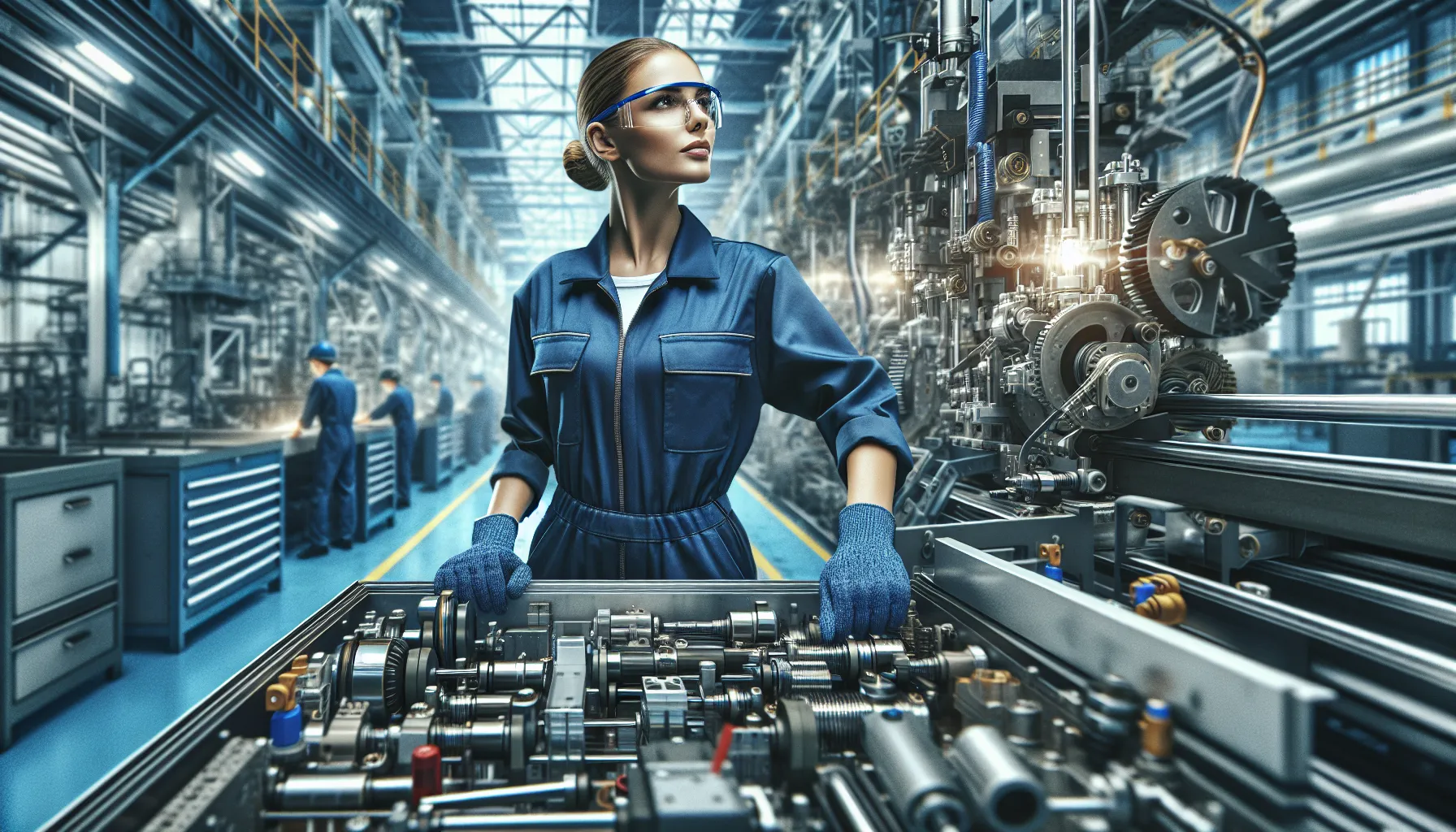
Spotting issues early helps me prevent costly downtime and extend equipment life. I focus on the most common problem areas that impact machinery performance.
Mechanical Failures and Breakdowns
Mechanical failures top my list of recurring industrial machinery issues. I watch for issues like worn bearings, misaligned shafts, and broken gears since they often cause sudden stoppages. I’ve seen loose belts and damaged couplings disrupt everything from conveyor systems to presses. Unusual noises, increased vibration, or excessive heat usually signal these problems before a full breakdown occurs.
Electrical System Malfunctions
Electrical system malfunctions frequently cause unexpected machine outages. I check for faulty wiring, blown fuses, and malfunctioning sensors since they often result in intermittent stops or erratic machinery behavior. In my experience, control panel issues and failed relays are common in automated equipment, leading to production errors and safety risks if left unchecked.
Hydraulic and Pneumatic System Problems
Hydraulic and pneumatic system problems impact machines that depend on pressurized fluids or air. I look for leaking hoses, worn seals, and pressure drops as clear signs of trouble in these systems. Inconsistent movement, loss of force, or sluggish actuators usually means there’s a blockage, contamination, or component failure. Regularly inspecting and servicing pumps, valves, and filters helps me catch these issues early.
Recognizing Signs That Indicate Machinery Needs Repair
I always watch for specific warning signals from my equipment to avoid unexpected breakdowns and production delays. Let me break down the three main signs that tell me when my industrial machinery needs attention.
Unusual Noises and Vibrations
I notice new clanking, grinding, or rattling sounds when something’s wrong. Machines like conveyor belts, pumps, and motors often develop these noises if bearings fail, gears misalign, or components loosen. I also feel excessive vibration in the floor or housing, which usually means misaligned shafts or unbalanced rotating parts. If these sounds or movements become louder or more frequent, I schedule an immediate inspection to prevent major failures.
Reduced Performance or Efficiency
I pay close attention if my equipment starts running slower or delivers inconsistent results. Reduced output or longer production cycles often indicate issues like clogged filters, insufficient lubrication, or electrical problems in controls. For example, if my hydraulic presses don’t generate full pressure or compressors take longer to reach their target PSI, I know it’s time for repair before things get worse. Tracking key performance metrics helps me spot these drops early.
Visible Wear and Tear
I regularly inspect surfaces for cracks, rust, oil leaks, or deformed components. Seeing frayed belts, worn gears, leaking seals, or chipped blades signals to me that internal parts may be at risk of failure. Hydraulic hoses with bulges or electrical wiring with exposed insulation always get my immediate attention. I replace or repair these damaged parts right away to keep my equipment reliable and safe.
Choosing the Right Tools and Equipment for Industrial Machinery Repair
Selecting the proper tools and equipment is critical for efficient and safe machinery repairs. I always ensure my toolbox is well-equipped before tackling any maintenance job.
Essential Hand Tools
Wrench sets provide the grip and torque I need for loosening or tightening bolts on pumps, motors, and valves. Screwdrivers with magnetic tips let me handle fasteners in tight spaces, especially when working on electrical panels or control boxes. Pliers—needle nose, locking, and slip-joint—help me grip, cut, or twist wires and components during part replacements. Hammers, both soft-faced and ball-peen, allow me to align machine parts or tap in stubborn pins without damaging surfaces. Allen keys (hex keys) are indispensable for adjusting set screws commonly found on couplings and machine guards.
Diagnostic and Testing Equipment
Multimeters are essential for checking voltage, current, and continuity in industrial electrical systems, letting me quickly pinpoint wiring or circuit errors. Vibration analyzers help me detect bearing wear and misalignment in rotating machinery, preventing bigger breakdowns. Infrared thermometers let me scan bearings, motors, and gearboxes to spot overheating before it leads to failure. Ultrasonic leak detectors make it easy for me to identify compressed air or hydraulic leaks that sabotage efficiency. Hydraulic pressure gauges give me instant readings for system troubleshooting in forklifts, presses, and production lines.
Following Safety Precautions During Industrial Machinery Repair
I always make safety my top priority when repairing any industrial machinery. By following strict precautions, I’m able to reduce the risk of workplace accidents and protect myself and my coworkers.
Personal Protective Equipment (PPE) Guidelines
I never begin repairs without proper PPE. I wear insulated gloves to guard against electrical shocks, safety goggles for eye protection, and ear protection in loud machine environments. I use steel-toed boots to shield my feet from dropped tools or heavy parts. For tasks involving chemicals or hazardous fluids, I add coveralls and face shields. I check my PPE for damage before every job, ensuring it’s always in top condition and fits well.
Lockout/Tagout Procedures
I use lockout/tagout (LOTO) procedures every time I service machinery. I disconnect and isolate all power sources before starting work. I lock switches and valves in the off position, attaching my personal lock and a clear tag that states I’m working on the equipment. I keep the key with me at all times. I always verify with a multimeter or tester that power is actually off before touching any components. I don’t remove my lock or tag until I’ve finished and it’s safe to restart the machine. This process is non-negotiable for preventing unexpected startups and protecting everyone on site.
Executing Preventative Maintenance to Reduce Industrial Machinery Repair Needs
Preventative maintenance keeps my industrial machinery running reliably and reduces breakdowns that lead to expensive repairs. I focus on routine inspections and proper care to catch issues early and keep equipment in peak condition.
Regular Inspection Schedules
I set clear inspection schedules for all core machines, using manufacturer recommendations as a baseline. I check critical components weekly and review electrical, hydraulic, and pneumatic systems monthly. I examine belts, bearings, seals, and wiring for early wear. By logging inspection results, I easily spot trends and know when to replace parts before failure disrupts production.
Lubrication and Cleaning Practices
I follow strict lubrication schedules for moving parts, including gears, chains, rollers, and bearings. I use recommended oils or greases and check reservoirs to prevent under- or over-lubrication. I clean machines after every shift to remove dust, debris, and residue that can accelerate wear or clog components. I also inspect lubrication points and clean filters to keep machinery efficiency high and maintenance needs low.
Selecting a Qualified Industrial Machinery Repair Service
Finding a skilled repair service is crucial for minimizing downtime and safeguarding expensive equipment. I always weigh credentials, experience, and ongoing support before allowing anyone to work on my machinery.
Certifications and Experience to Look For
I always prioritize repair providers with certified technicians. Look for credentials like ISO 9001, OSHA training, and manufacturer certifications for brands in your facility. Experienced teams who’ve worked five or more years on comparable machines—such as CNC mills, injection molding equipment, and industrial HVAC systems—can often troubleshoot quicker and more accurately. These providers usually know industry regulations and follow current best practices for workplace safety, which protects both my staff and my investment.
Service Agreements and Warranties
I insist on clear service agreements with defined response times and transparent pricing. Comprehensive contracts address scheduled maintenance, emergency calls, and turnaround guarantees. I choose repair services offering at least 6-12 month warranties on labor and replacement parts for repairs on gearboxes, pumps, motors, and other core components. Reputable providers stand behind their work, so if a part fails or if workmanship causes an issue, I know they’ll return to fix it without extra charges. This support gives me peace of mind for both daily operation and long-term planning.
Embracing Emerging Technologies in Industrial Machinery Repair
Staying competitive means leveraging the latest tools for industrial machinery repair. I rely on new technologies that help me spot problems faster and reduce unexpected downtime.
Predictive Maintenance and IoT Sensors
I use predictive maintenance to fix issues before breakdowns happen. Smart IoT sensors track machine temperature, vibration, and pressure in real time. For example, I install wireless sensors on motors and pumps that send alerts the moment something changes—helping me intervene early. According to Deloitte, factories using predictive systems see up to 30% lower maintenance costs and 70% fewer breakdowns. By gathering continuous data, I schedule repairs only when needed, optimizing parts usage and extending equipment life.
Technology | Function | Reported Benefit |
---|---|---|
IoT Vibration Sensor | Monitors abnormal vibrations | Prevents bearing failures |
Thermal Sensor | Tracks overheating components | Reduces unexpected stops |
Pressure Sensor | Checks for leaks/clogs | Detects hydraulic issues |
Remote Monitoring and Diagnostics
I streamline repair planning by tapping into remote monitoring tools. These systems let me view equipment status and receive alerts, sometimes via mobile apps or cloud dashboards. If a pump sends high-temperature warnings, I know before stepping foot on the shop floor. Diagnostic software can pinpoint faults using machine logs and sensor data. This approach helps me avoid major downtime and ensures repairs are targeted. I’ve found remote access allows experts—even offsite—to troubleshoot problems instantly, which speeds up complex repairs and keeps production moving.
Conclusion
Industrial machinery repair is more than just a technical task for me—it’s a critical part of keeping my operations running smoothly and efficiently. By staying proactive and investing in the right tools, safety practices, and repair partners, I can keep downtime to a minimum and protect my equipment for years to come.
Embracing new technology and prioritizing routine care not only boosts productivity but also gives me confidence that I’m prepared for any challenge my machinery might face.
Frequently Asked Questions
Why is timely industrial machinery repair important?
Timely industrial machinery repair prevents unexpected downtime, reduces costly production delays, and ensures equipment operates efficiently. Addressing issues quickly also extends the lifespan of your machinery and maintains workplace safety.
What are common signs that machinery needs repair?
Look for unusual noises, excessive vibrations, reduced performance, and visible wear or damage. These warning signs often indicate underlying issues that need immediate attention to avoid bigger failures and downtime.
How can regular maintenance extend machinery lifespan?
Routine maintenance, including lubrication, part replacement, and inspections, keeps machinery running smoothly. It helps spot potential problems early, preventing major breakdowns and supporting long-term equipment reliability.
What are typical causes of industrial machinery failures?
Common causes include mechanical failures (e.g., worn bearings), electrical malfunctions (e.g., faulty wiring), and hydraulic or pneumatic issues (e.g., leaking valves or blocked filters). Early identification and repair help prevent serious disruptions.
Which tools are essential for industrial machinery repair?
Core hand tools like wrench sets, screwdrivers, pliers, hammers, and Allen keys are essential. Diagnostic tools such as multimeters, vibration analyzers, infrared thermometers, and hydraulic pressure gauges help accurately troubleshoot and repair machinery.
What safety precautions should be taken during repairs?
Always use proper personal protective equipment (PPE), including gloves, goggles, ear protection, and steel-toed boots. Follow lockout/tagout (LOTO) procedures to fully isolate equipment from power sources before starting any repair.
How often should industrial machinery be inspected?
Inspect critical machines weekly for wear and damage. Review electrical, hydraulic, and pneumatic systems at least monthly. Logging inspection results helps track issues and plan preventative maintenance more effectively.
What is predictive maintenance and why is it valuable?
Predictive maintenance uses real-time IoT sensors and diagnostic software to monitor machine conditions and predict failures before they happen. This approach reduces unexpected downtime, lowers maintenance costs, and minimizes production losses.
How do I choose the right industrial machinery repair service?
Look for providers with certified technicians and relevant industry experience. Ensure they offer quick response times, clear service agreements, and warranties. Reputable repair services offer reliability, reduce downtime, and protect your investment.